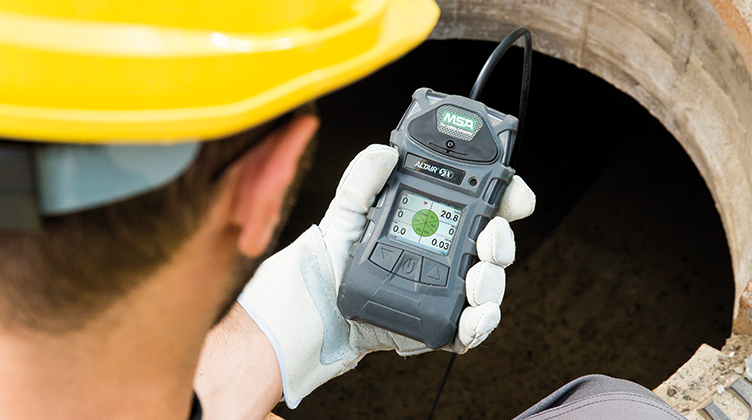
Gas detection equipment is a vital safety device in a variety of industries. They are designed to detect combustible and toxic gases, preventing potential harm to employees and the environment.
There are many types of industrial gas detectors, each with a different operating principle. Choosing the right one for your requirements is crucial to protecting your employees.
Infrared (IR) Sensors
Infrared (IR) sensors are used in a wide range of applications. They use IR light to detect gases that absorb the IR light at characteristic wavelengths. The IR beams of light from an emitter within the sensor are split and sent through filters to a photo receiver which measures the difference in intensity between the two beams. Hydrocarbon gas molecules absorb the “measuring” beam, and the intensity of this beam is reduced, while the gas does not absorb the “reference” beam, so arrives at the receiver at full strength.
The IR measurement signal detector receives the measured drop in the intensity of the “measuring” beam, which is compared to the reference output of the detector to determine the amount of hydrocarbon gas present. This process is very fast and accurate, typically less than 10 seconds.
Unlike other types of detectors and gas particle analyzers, IR sensors do not require routine calibration or maintenance. They can operate in oxygen-rich or oxygen-poor environments. They are highly immune to poisoning, oxidation, or corrosion.
They are also very reliable. They can be operated with minimal power, even in high temperatures. They can be positioned in inaccessible areas.
A major advantage of IR detectors is that they do not require routine maintenance like catalytic devices. This makes them very attractive to a number of industries. They are not subject to the usual maintenance issues of gas detectors, such as the need for routine calibration, and they can be repaired in the field by a factory technician.
Infrared sensors are also very cost-effective. They typically have a higher initial cost than catalytic devices at the time of purchase, but they are rapidly reducing in price. They are more susceptible to the impact of environmental conditions such as humidity and dusty fields, but a low-maintenance approach can mitigate this.
They are also less sensitive to hydrogen than other gas detection devices, but this is not a significant problem as most instrument manufacturers promote the use of a “cross interference” to hydrogen on the CO sensor in order to overcome the lack of hydrogen detection capability on a single sensor.
Pellistor/Catalytic Bead (PCB) Sensors
Pellistor/catalytic bead (PCB) sensors are a common choice for flammable gas detection because they provide accurate, reliable and affordable detection. They are also easy to maintain and have an extremely wide range of applications.
These sensors work by coating a catalytic bead with a catalyst. This causes combustible gases to burn at lower concentrations and temperatures than an untreated bead. A reference bead or compensator is not coated with a catalyst. This allows the sensor to detect a variety of different combustible gases.
However, certain compounds that decompose on the bead surface can poison the catalytic bead catalyst. This can cause a loss of sensitivity and damage the sensor. Poisoning is not permanent and can be resolved by a bump test or calibration.
Some pellistor sensors are equipped with filters that limit exposure to vapors or gases that could impact the bead catalyst. This can make the sensor less sensitive to heavy hydrocarbons.
Additionally, the bead can be protected from contaminants such as lead and silicone. These can cause a buildup of oxidants on the bead, which can also reduce its sensitivity.
The resistance of the bead is measured in a series of measurements at different time intervals, using different gases, and at different temperatures. This gives the user an idea of how the sensor reacts under various conditions.
For example, if the sensor is used in a high-pressure environment, the resistance will change more rapidly than if it was in a low-pressure environment. This can allow the researcher to identify which parameters are important for the sensor response.
In addition, the resistance can be changed to a different value at a specific time by applying an external analyte gas. The resulting change in resistance is then compared to the response of the sensor under a controlled setup.
As part of gas detection research, it is becoming more and more standard to fully control and maintain the temperature, gas flow through the chamber, and the humidity of the sensors as they operate. This allows the researcher to observe the influence of these variables on the sensor response over time and to understand the mechanism of these changes.
Gas Sensitive Film (GSF) Sensors
When a substance molecule (for example, volatile organic compounds, or VOCs) or a volatile sulfur compound molecule (for example, H2S) contacts an adsorbent (a material that absorbs the chemical), the surface of the adsorbent changes its electrical properties. The variations in the electrical resistance allow one to determine the concentration of the substance. These devices are known as chemiresistors or polymeric gas sensors.
Several methods for depositing these thin film materials have been reported, including magnetron sputtering [5,6,7], sol-gel, chemical vapor deposition, ultrasonic spray pyrolysis, and atomic layer deposition. All of these methods involve sequential alternative dosing of chemical precursors that chemisorb to the substrate. The resulting adsorbents are highly conformal and self-limiting in nature, forming a single thick film at the surface of the substrate.
The most common approach to improving the response characteristics of SAW sensors to gases is to enhance their anti-interference ability. This is done by increasing the adsorbent’s specific surface area and active sites, which will reduce its affinity for a particular gas. Other approaches that have been used include adding noble metal additives that have high-effective oxidation catalytic activity. These catalysts may be deposited on the adsorbent surface, e.g. a Pd-Pt/SnO2 composite film was developed as an example of this technique.
Another method of improving the sensitivity to trace gases involves increasing the frequency response performance of the sensor by improving its response time. This is a method that has been successfully applied to many gas sensing applications, including ozone sensors and carbon monoxide gas sensors based on a Pd-Pt/SnO2 sensitive film.
In addition, the use of multiple electrodes can increase the sensitivity to low-level gas concentrations. This is especially useful in detecting CO gas, which tends to have a high-frequency response.
In addition, the sensor’s stability under the test conditions is also an important factor. For example, if a sensor is used repeatedly to test a CO gas with a concentration of 30 ppm over a period of 30 days, the frequency response fluctuation will be lower than 5%, indicating good long-term stability for the CO gas.
Metal Oxide Semiconductor (MOS) Sensors
The most common type of gas sensors are metal oxide semiconductor (MOS) sensors. These devices have a reversible reaction between the gas and the solid-state surface of the sensor, allowing it to detect gases using conductivity, capacitance, work function, mass, or optical properties.
The performance of MOS sensors can be enhanced by controlling their catalytic activity at the surface, which is the main source of the sensor’s conductivity response. Moreover, working temperatures and crystal defects also affect the gas sensitivity of these materials. For example, adsorption of the target gases at a low temperature could cause the crystal defects to open, increasing the sensor’s sensitivity.
In addition, the electronic configurations of the sensing material can also be controlled to improve its sensitivity and selectivity, which is usually achieved by using a different number of n-n or p-p heterojunctions. For n-n heterojunctions, the number of n-n recombination can significantly affect the sensing response, whereas for p-p heterojunctions, the number of p-p recombination can also significantly affect the sensitivity.
Another important way to enhance the sensitivity of the sensor is to grow heteronanostructures on the MOS-based sensor and control their size, thickness, and morphology. This is particularly beneficial in the fabrication of gas sensors on patterned microchips, where it is essential to precisely control the size and structure of the sensing materials.
Heteronanostructure-based gas sensors are a promising platform for the next generation of durable conductometric gas sensors due to their open surface, high gas sensitivity, and long-term stability. However, the sensitivity of these sensors can be affected by many factors, such as molar ratios of the two n-n or p-p recombination materials and their semiconductor types.
To further enhance the sensitivity of these sensors, new strategies to grow heteronanostructures on a patterned microchip are needed. Specifically, it is crucial to develop techniques for growing MOS heteronanostructures at specific locations on the microchip and precisely controlling their size, thickness, and morphology. These strategies will help to eliminate aggregation of the sensing materials and ensure the reproducibility of these sensors. This will be critical for the large-scale fabrication of these sensors.